EN14399 Structural Nuts Price - ASTM A320 L7 All Threaded Stud Bolts – Dingshen Metalworks
Short Description:
ASTM A320/A320M L7 All Threaded Stud Bolts Alloy steel bolting for pressure vessels, valves, flanges, and fittings for low-temperature service. Standard: IFI-136, ASME B16.5, DIN976 Inch Size: 1/4”-2.1/2” with various lengths Metric Size: M6-M64 with various lengths Other Available Grade: ASTM A193/A193M B7, B7M, B16 B8 Class 1 & 2, B8M Class 1 & 2, ASTM A320/A320M L7, L7M, L43, B8 Class 1 & 2, B8M Class 1 & 2, and so on. Finish: Plain, Black Oxide, Zinc Plated, Zinc Nickel Pl...
Product Detail
Product Tags
EN14399 Structural Nuts Price - ASTM A320 L7 All Threaded Stud Bolts – Dingshen Metalworks Detail:
ASTM A320/A320M L7 All Threaded Stud Bolts
Alloy steel bolting for pressure vessels, valves, flanges, and fittings for low-temperature service.
Standard: IFI-136, ASME B16.5, DIN976
Inch Size: 1/4”-2.1/2” with various lengths
Metric Size: M6-M64 with various lengths
Other Available Grade:
ASTM A193/A193M B7, B7M, B16 B8 Class 1 & 2, B8M Class 1 & 2,
ASTM A320/A320M L7, L7M, L43, B8 Class 1 & 2, B8M Class 1 & 2, and so on.
Finish: Plain, Black Oxide, Zinc Plated, Zinc Nickel Plated, Cadmium Plated, PTFE etc.
Packing: Bulk about 25 kgs each carton, 36 cartons each pallet
Advantage: High Quality and Strict Quality Control, Competitive Price,Timely Delivery; Technical Support, Supply Test Reports
Please feel free to contact us for more details.
Product detail pictures:

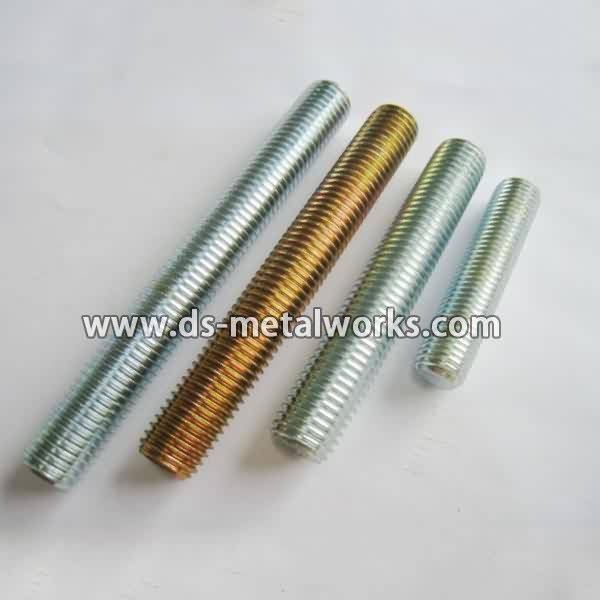

It is actually our accountability to satisfy your needs and effectively serve you. Your pleasure is our best reward. We're on the lookout forward for your stop by for joint growth for EN14399 Structural Nuts Price - ASTM A320 L7 All Threaded Stud Bolts – Dingshen Metalworks, The product will supply to all over the world, such as: Stuttgart, Toronto, Jamaica, Over the years, with high-quality solutions, first- class service, ultra-low prices we win thee trust and favor of customers. Nowadays our products sell all over the domestic and abroad. Thanks for the regular and new customers support. We offer high quality product and competitive price, welcome the regular and new customers cooperate with us!
***! TRY THIS AT YOUR OWN RISK !****(still awaiting a period of “field testing” for these).
Energy Suspension bushing and inner sleeve installation without the use of a hydraulic press; just some hardware, a wrench, a socket and an air-powered impact gun.
Borrowed the idea and gained some more confidence for this installation process after watching GallowayChicago’s bushing install video; thanks man.
I tried to install the bushings using the bolt-press method, but the bushing would not quite fit– it would just compress and then when a little bit of the leading edge would go in, it would slip out and go crooked within the bolt-press jig.
I added relief cuts along the edge (one at a time across from each other; 6 was the min # that worked) after taking a cue from what appeared to be a relief spot in all of the bushings on the leading side (side that goes into the link or arm socket first; this side also appeared to have a tiny bit more taper than the other side as well). I started by making this relief deeper, then started adding slots, just as deep as the edge, being careful not to cut into the main cylindrical part of the bushing.
Materials:
1x- threaded rod (want this to be very close to the inner diameter of the metal sleeve insert of the bushings; length just needs to be long enough to fit the whole bolt-press-jig assembly together- so length of bushing + length of link/suspension arm socket + all other hardware thickness)
2x- grade 8 hex nuts
2x- large washers (want these to be able to cover and be a little larger than the largest diameter of the bushing, so the edge of the washer doesn’t cut into the bushing and the washer will help distribute the force exerted by tightening the nuts on the “bolt press jig”
2x-washers appropriately sized for the hex nuts being used (mentioned above)
*multiple washers between the sizes (2 of each, one for each side of the bolt press jig); just used to properly transition between the two other washer sizes used (large against bushing and hex-bolt-sized against the hex nut
- lots of appropriate type of grease, depending on what the bushings are made of (thankfully most Energy Suspension bushings come with just the right amount of “polyurethane-safe” grease.
Tools:
-compressed air source
-impact gun
-sockets for hex nuts
-adjustable or crescent wrench for hex nuts
- small saw or dremel with rotary cutting wheel
Steps:
1. using the small saw or dremel with cutting wheel make cuts perpendicular to the apex of the bushing surface, ONLY on the outer edge, being careful not to cut into the main cylinder body of the bushing; again just on the edge- this is only to provide enough “flex” for this larger outer edge to tuck and go through the link/ suspension arm’s socket.
2. put a hex nut on the threaded rod so that the nut fully threads on it, but only protrudes a slight amount if any, then the multiple sizes of washers small to large (consider space restrictions; may have to put rod through the link/suspension arm socket first and then start assembly of the jig; may have to thread the rod even further than just “fully seated” on the hex nut on the one side).
3. Put the threaded rod through the bushing on the opposite side of the link/ suspension arm socket, then stack the washers on top from large to small, followed by the hex nut
4. Grease EVERYTHING- lots of grease: inside link/ suspension arm socket, on leading face (slotted side) of bushing and the bushings exterior surfaces
5. Using impact gun (bushing side) and using wrench on opposite side, drive the hex nut down on the bushing side. May have to go slow at first to get the edges aligned and then just fully drive it in. The bushing will not go fully in, but just drive the hex nut tighter until no more forward progress is made.
6. Disassemble the jig and repeat the process for the inner sleeve (remember grease everything!). This time the inner sleeve should push the leading edge of the bushing fully through the link/suspension arm’s socket as long as there was plenty of grease available; if not, one can gently pry out the other side with an appropriate tool
*Tip: found the grease included with these is best removed from tools with a two step process: first WD-40, then Brake cleaner to remove the WD-40
Hope this helps. If anyone has any questions, please free to ask.
Hey y’all! After mulling a metric butt-ton of videos, sound clips and forums on this topic, I decided to go ahead and finish my upgrades on my Strat with a Brass Sustain Block and Graphtech saddles & do my own video showing my findings.
Let your ears hear it for yourself. I wanted to hear NOTHING but the changes on the guitar, so I changed none of the recording settings, I put the same strings back on the guitar, before disassembly I noted the string heights and setup with a dial indicator, and set it back up within +/- .002″. I think this is as close as comparing apples to apples as one can get.
I didn’t want any room reflections or anything else get in the way, so I plugged direct into an Eleven Rack running the 64 Vibro Clean sim stereo straight into Logic Pro X. Knowing the differences would be subtle, i opted to do a clean tone so not to bury the changes in gain. But to keep it ‘real world’, knowing most people run a bit of chorus, delay and or reverb, I did include those effects.
Here is my line of thought on why I did this the way I did it.
a) it seems most people talked about the changes affecting the notes ‘attack’ and ‘sustain’, therefore I chose to do a clean-tone with arpeggiated chords and a ringing chord to follow.
b) It drove me crazy with the ‘before and after’ sounds being so far apart, so I cut and pasted this together so it was “bridge pickup-zink and stamped steel” followed by “bridge pickup – brass and Graphtech”, then I moved on to position 2, 3, 4 and lastly 5.
c) Again, i wanted this to be a straight forward apple to apple comparison, so I touched NOTHING on the settings from the 2 takes.
Here is what I found.
a) The difference is very subtle. In many cases, because I had the tone controls kind of dialed in for the zink and stamped steel, you may think that combination sounds “better”, but hear me out before you make that decision.
b) The attack of the notes are just a tad more compressed. I actually didn’t fully grasp that until i went back and looked at the wave forms when i was editing the audio. There is not as much spike overall on the initial attack. That is not to say that there are and will be inconsistencies due to the human factor applying the pick angle and attack.
b) its not so much that the sustain is MORE … if you are familiar with audio editing, and applying fade outs, it changes the slope of the fade (decay) … it doesn’t drop as far as fast right off the bat. Again, this became more apparent after I started editing the audio and was LOOKING at the wave shapes.
c) after spending a couple hours playing with it, i did notice ONE thing that was more apparent .. and it took me a while to catch this. I set my Strat up with the bridge sitting on the deck (which people STILL said you WOULD hear a difference in TONE .. yeah, not so much) … BUT .. when using the Trem, when you bring that bridge off the deck, it did not have the tonal difference AS much … thats a good thing! But, it took me a while to catch that. Again, it isn’t huge, but its there!
d) the guitar is a little more resonant to play unplugged, it does feel a little more lively in hand and with the brass being a good 30% heavier than the zink, it gives the weight and balance a nice center point.
e) The more i play it, I do hear that the individual notes do ring more balanced within a chord.
So, with that being said … in conclusion after a couple hours playing and tweaking, are the differences worth it? I find that dialing in sweet spots a little easier. After tweaking settings, you can find better, sweeter tones within your amps dials. It gives you more useable range to play with. It has me wondering now, if all the upgrades i did previous to these last 2 maybe did not let me see as BIG as a difference as I thought i would. Time will tell … maybe I’ll go back to stock, and start doing videos one mod at a time …
The guitar: 2008 Fender Stratocaster Std (Mexico) 48th St Special Edition in Graffiti Yellow.
The Mods: Schaller Locking Tuners, Roller String Tree, Graphtech nut, Floyd Rose brass spring claw/screws, Floyd Rose high tension low noise springs, GFS Brass block, Graphtech saddles, full cavity shielding with copper tape, David Allen “Dover” pickups, ‘vintage style’ cloth push back wire, CTS pots, CTS 5way switch. I leveled and polished the top of the brass block and the bottom of the bridge to insure as close to 100% coupling as I could, for maximum resonance transfer. In the process of going with a ‘satin’ look on the hardware, I sanded about 50% of the chrome off the bridge (if you think that provides a tonal difference, Ive never heard it tho)
The setup: Guitar plugged directly into Avid Eleven Rack, 64 Vibro Champ amp sim, chorus, delay and reverb added. Recorded a direct stereo line out of that into Logic Pro X on a 27″ iMac, 3.1Ghz Intel Core i5, 16G RAM.